MRP
Material Requirements Planning 資材所要量計画
Material Requirements Planningの略で、一般に資材所要量計画といわれる。MRPは、1970年「アメリカ生産・在庫管理協会」、略称APICS(American Production and Inventory Control Society)の提唱により、急速にその活用が広まった資材計画の1手法である。この方法では、図に示すように、立案された製品レベルの生産計画を基に、組立品、部品、原材料などの従属需要品目について"必要なものを(品目)、必要なときに(納期)、必要なだけ(所要量)"購買したり、製造したりするための手配計画を行う。このように、従属需要品目の手配計画を作成するために、MRPは大きく3つの情報を必要とする。
● 生産計画:製品やサービスパーツなど独立需要品目の生産計画で、基準生産計画とかMaster Production Schedule を略してMPSとか呼ばれる。MRPはこの計画を基に従属需要品目の計画を行う。
● 部品表:独立需要品目から従属需要品目へ、従属需要品目の中でも組立品から原 P.45 材料へと使用品目の洗い出し(展開)が必要となる。このために部品表は用いられる。なお、部品表には、原単位、リードタイム、ロットサイズなど資材計画に必要な基礎情報が設定されていなければならない。
● 在庫・注残:算出された各従属需要品目の所要量を基に正味所要量を算出するために現在庫、注残、仕掛などの在庫・注残情報を必要とする。
このような情報を基に、MRPは次の5つの機能を実行して、従属需要品目の手配計画を行う。
● 総所要量計算:各々の従属需要品目の要求されている量を、ある期間単位にまとめて、期間別の総所要量を算出する。
● 正味所要量計算:算出された総所要量を基に在庫や注残への引当を行い、期間別に必要な正味所要量を算出する。
● ロットまとめ:算出された期間別の正味所要量を基に、品目に設定されているロットサイズを用いて、手配に最も適した数量にまとめる。
● リードタイム計算:ロットまとめされた数量の納期からリードタイムを差引き、その発注日または着手日を算出し、オーダーを作成する。
● 所要量展開:部品表を用いて作成したオーダーの下位品目へと展開し、製品構成に設定されている原単位を参照して、展開された品目の所要量を算出する。
この5つの機能を上位品目から順に、レベル・バイ・レベルですべての従属需要品目について行い、最下位の品目の処理が終了した段階でMRPは終了する。
Material Requirements Planningの略で、一般に資材所要量計画といわれる。MRPは、1970年「アメリカ生産・在庫管理協会」、略称APICS(American Production and Inventory Control Society)の提唱により、急速にその活用が広まった資材計画の1手法である。この方法では、図に示すように、立案された製品レベルの生産計画を基に、組立品、部品、原材料などの従属需要品目について"必要なものを(品目)、必要なときに(納期)、必要なだけ(所要量)"購買したり、製造したりするための手配計画を行う。このように、従属需要品目の手配計画を作成するために、MRPは大きく3つの情報を必要とする。
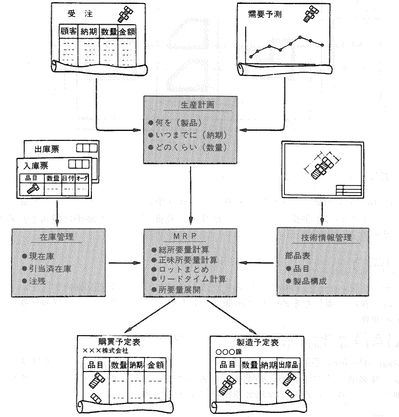
● 部品表:独立需要品目から従属需要品目へ、従属需要品目の中でも組立品から原 P.45 材料へと使用品目の洗い出し(展開)が必要となる。このために部品表は用いられる。なお、部品表には、原単位、リードタイム、ロットサイズなど資材計画に必要な基礎情報が設定されていなければならない。
● 在庫・注残:算出された各従属需要品目の所要量を基に正味所要量を算出するために現在庫、注残、仕掛などの在庫・注残情報を必要とする。
このような情報を基に、MRPは次の5つの機能を実行して、従属需要品目の手配計画を行う。
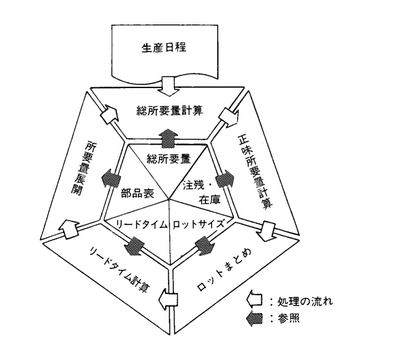
● 正味所要量計算:算出された総所要量を基に在庫や注残への引当を行い、期間別に必要な正味所要量を算出する。
● ロットまとめ:算出された期間別の正味所要量を基に、品目に設定されているロットサイズを用いて、手配に最も適した数量にまとめる。
● リードタイム計算:ロットまとめされた数量の納期からリードタイムを差引き、その発注日または着手日を算出し、オーダーを作成する。
● 所要量展開:部品表を用いて作成したオーダーの下位品目へと展開し、製品構成に設定されている原単位を参照して、展開された品目の所要量を算出する。
この5つの機能を上位品目から順に、レベル・バイ・レベルですべての従属需要品目について行い、最下位の品目の処理が終了した段階でMRPは終了する。